The Little Pour on the Prairie: Transforming Iron Into Art
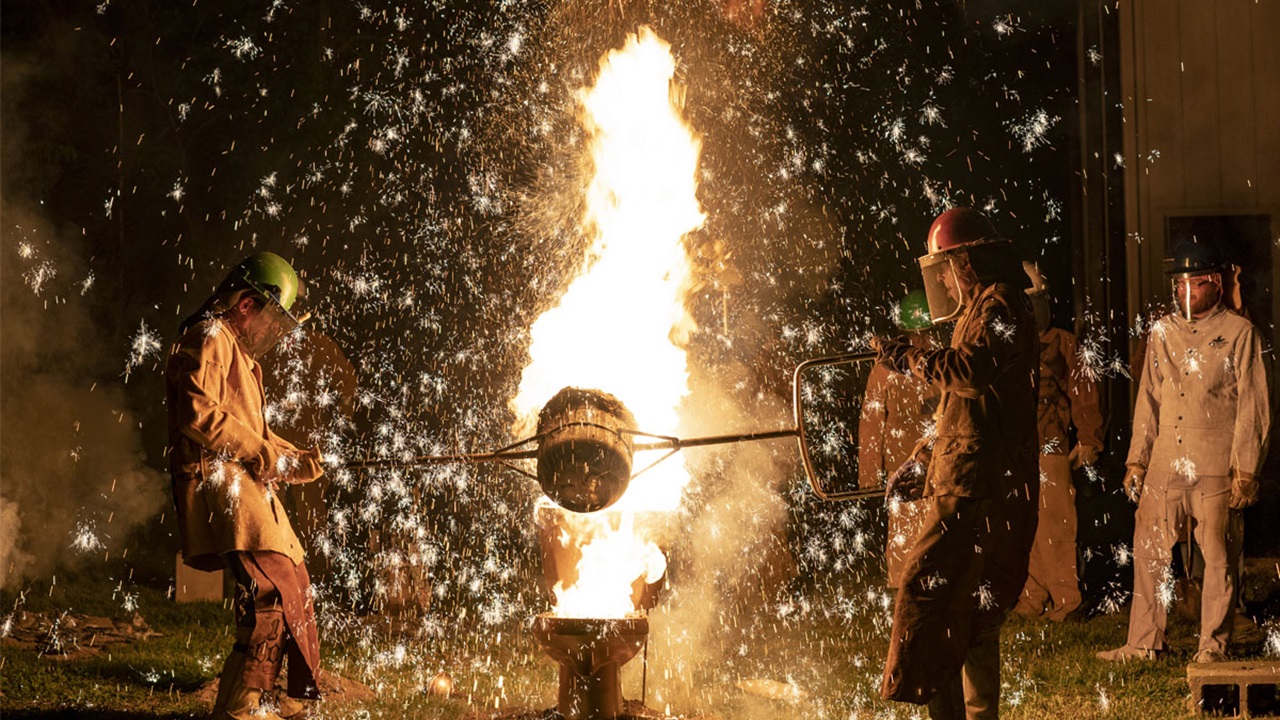
Chris Meyer, an associate professor of sculpture who has taught at the University of South Dakota since 2006, hosts the Little Pour on the Prairie at his 14-acre farm northwest of Vermillion, where attendees can camp out on his land and participate in the pour. “It’s usually a pretty relaxed time,” said Meyer. “It’s about community, a gathering of artists.”
The Little Pour begins in the Warren M. Lee Center for the Fine Arts building on USD’s campus. Meyer ’00, holds workshops where participants can make molds to take to the farm. Once there, attendees participate in a production pour, where molten iron is poured into sand or ceramic shell molds; alternately, they can do a performance pour with reaction molds or other means of iron performance.
At Meyer’s farm, the Little Pour on the Prairie starts with the pouring of production molds before dusk and finishes with the performance pour after dark, creating a spectacular show of flames and sparks.
“A reaction mold is a mold that is made out of, or includes, non-refractory materials, which react with the molten iron burning, splattering and possibly exploding,” Meyer said. “Working with reaction molds requires one to give up a certain amount of control over the outcome or final product; you can never be certain of how the reaction may unfold or what the resulting form will look like.
“The intent for these molds is twofold: to create a vigorous visual reaction as part of the spectacle of a performance pour and to produce a successful and dynamic casting,” he continued.
After all the creations have cooled and solidified, participants open the molds to reveal their beautiful and unique designs.
For Tasha Determan, a junior fine arts major specializing in sculpture and an honors student, the unknown outcome of iron pouring is exciting.
“I like the nature of working with other sculptors in order to make art and working with them in a precarious interaction,” she said. “The sparks are really beautiful and really hot.”
It’s not just the sights of the finished product that are beautiful, however—there is also beauty in the process.
In order to melt the iron, it first has to be broken down to the size of playing cards. They use radiators, pipe, sinks, bathtubs—any iron, Meyer said, that is thin enough to break down.
“Most of our iron scrap has been donated to us or scrounged up by myself and students. State Steel in Sioux City has donated drop steel to make tools and other art, and they also donate stove cast scrap iron from Sioux City Compressed Steel Co. We are always looking for scrap iron and other metals to recycle into art,” Meyer said.
After breaking down the iron, it has to be weighed.
“You have to think about the size of the furnace, the weight of the charges of iron, as well as the charges of coke [the fuel used to heat the iron]. There is some math involved,” said Meyer. “Then when you’ve figured out the math, you have to learn the machine. The more you run it, the more experience and knowledge you gain. Every pour is a little bit different, but you learn the variables.”
Hunter Smith, a graduate student in the sculpture program with an emphasis in foundry technique, said the means in which they get ready for a pour is ritualistic.
“It takes a certain process to get it going compared to an average crucible foundry pour in-house. It takes a lot of preparation and forethought; it feels like a big thing that’s going to happen. It always feels magical in a way,” Smith said.
USD also had to have its own furnace to melt the iron. “Patches,” USD’s affectionately named furnace, was built by Meyer and Jordan Eaton ’13 B.F.A. (sculpture), designed to be put together without heavy machinery.
“There’s a lot of math involved to figure out volumes, cubic feet and air flow just to build a furnace that works,” Meyer said. “We do a lot of blacksmithing, welding and fabrication."
“It’s a lot of fun learning about the process,” Determan said. “There’s so much science behind it, I haven’t really learned about everything yet.”
Though the process is arduous, the outcome is magnificent.
“It’s a thrill,” David Barnum, a graduate student in the sculpture program, said. “You want it to be spectacular for the audience, but you are also trying to create ways for cast iron to flow in the reactions. You’re creating a piece that has life to it.”
The Little Pour on the Prairie got its start five years ago with Meyer and a few of his students.
“There are several iron programs across the country. They tend to be more in concentrated areas where industry has been predominant for cast iron; the south and the northeast around Pennsylvania and New York,” Meyer said. “But in the west, it is so spread out. A coalition of cast iron artists and educators has been trying to make happen in the west what was already happening in the east.”
Because iron programs are spread out around the country, cast iron artists bring their work with them to attend iron pours. Through the travel, Meyer said he has gotten to know a community of casters. “They’re kind of like family. We’re like a band of gypsies almost—some of us are educators, others are artists,” he said.
Meyer has brought students with him to some of the national pours. It was at the Second Biennial Western Cast Iron Conference in Missoula, Montana, in 2010 that Meyer became fascinated with the process. Then, two years later, he attended the same conference in Hayes, Kansas, with a larger group of students and got more excited about iron pouring. When they returned, they decided to build a furnace.
“It took a while to get our materials and everything together, as well as to research what we needed to do,” Meyer said. “We built the furnace and hosted a visiting artist to test our equipment, the furnace and all our tools at my farm.”
In the summer of 2014, Meyer and a few current and former students made molds and took everything to his farm. They also invited iron casting friends from Minnesota to help. “They were cast iron artists who could help us with our maiden voyage,” Meyer said. “And that spurred on the Little Pour on the Prairie. It mostly started off with them, my current students and some former students.”
This year, the Little Pour had participants from nine different states from as far away as Oregon.
“The Little Pour on the Prairie is a lot of fun,” Smith said. “In a lot of ways it seems to me that it’s a celebration of the history of sculpture at USD. There seems to be a lot of heritage within it. From Chris’s first graduate students to everyone he has taught, there’s a pretty good chance you’re going to meet them out there. It’s definitely like the heart and soul of the sculpture program in and of itself.
“It’s the ‘who’s who’ in the active art community,” he said.
Smith has attended the Little Pour since 2015, before he was a student at USD.
“My sculpture teacher at Black Hills State University was one of Chris’s first graduate students, and she told us about the Little Pour,” Smith said. “We didn’t know what to expect. I had no concept of any of it at the time, and it was all so foreign to me. It was amazing.”
This year was also the first time there were two furnaces at the Little Pour. Patches was joined by the only other furnace in South Dakota, built by Eaton, who now works at Bronze Age Art Casting LLC in Sioux Falls.
Anyone can participate in the Little Pour.
“It’s up to anyone for how involved they want to be, which I think is pretty unique. Even if you’re not an art student, you can pour iron. Chris is such a good teacher, it takes no time at all to train people,” Smith said.
“Students are exposed to several cast iron artists and other art students from across the region and country, and they get to see the work being created and cast by these artists and discuss ideas,” added Meyer. “They get a chance to learn other methods of moldmaking and furnace operation, and they make networking connections for graduate school or even employment opportunities. Students get to have fun working together and making connections with other cast iron artists from beyond USD, thus becoming a part of a larger cast iron art community.”
Iron pouring requires a community willing to gather and create art, as well as to help with the heavy lifting.
“Traditionally, cast iron is a less expensive metal to cast, but it is much more physically demanding,” Meyer said. “We have to work together to have an iron pour and we have to help others with less experience build molds and on the pour floor, which creates a strong bond among iron casters.
“It depends on everyone helping out, coming together and coordinating together,” Meyer said.